Produção de peças por processos híbridos
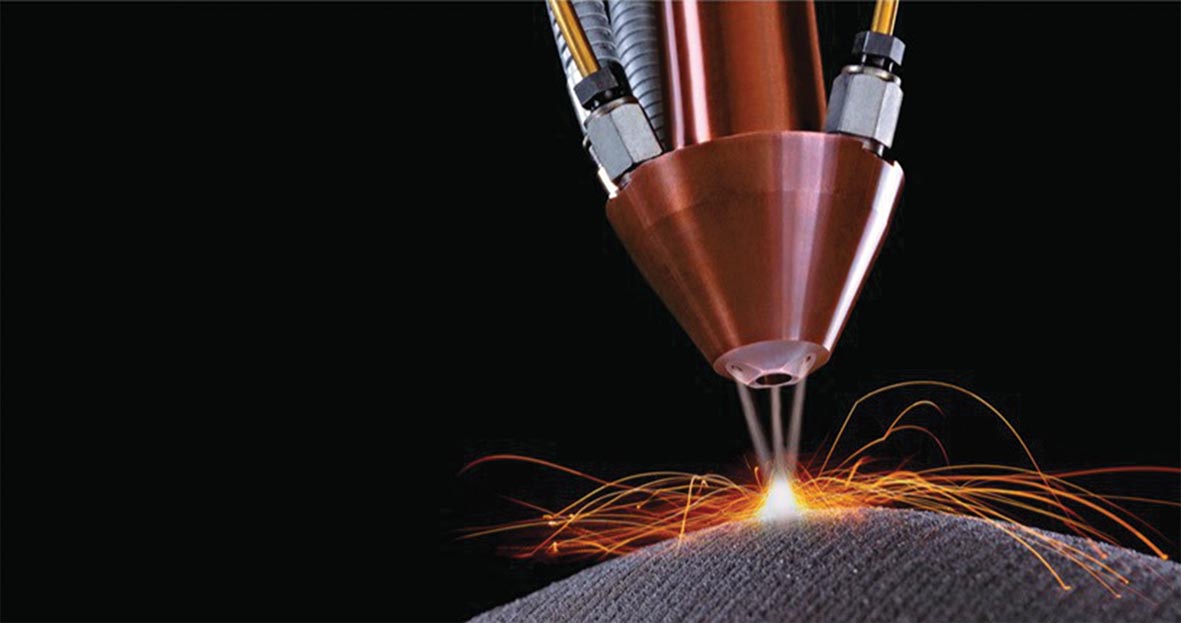
28.03.2016
Hoje existem equipamentos que somam o melhor das tecnologias subtrativas (arranque de lascas) e aditivas (aporte de materiais), alcançando ótimas soluções de frente para um mundo que exige cada vez mais precisão, eficiência e por sua vez flexibilidade e customização. Nesta nota fazemos uma breve revisão da fabricação de aditivados, as soluções híbridas que são incorporadas à mecanização, suas vantagens e os desafios a serem superados para que se consolidem.
Em primeiro lugar, vamos fazer uma breve revisão de como chegamos a este tipo de equipamento, seus antecedentes e as enormes perspectivas que esta tecnologia apresenta para um futuro próximo. Muitos especialistas se atreveram a falar de uma nova revolução industrial!
Bem, vamos começar. Faremos alguns esclarecimentos para quem não esteja familiarizado com estes termos. Quando falamos de tecnologias aditivas nos referimos a diferentes sistemas que aportam material para a escala micrométrica, depositando-o de forma muito precisa para construir um sólido. O conceito nasce da impressão 3D há aproximadamente 30 anos, quando surgiam os primeiros equipamentos experimentais que permitiram produzir peças de materiais plásticos alcançados por acumulação de fios de material aportado por um cabeçal “injetor” a partir de um design digital do tipo CAD. Os resultados eram surpreendentes desde o ponto de vista conceitual –“criamos um produto tridimensional, do nada”- mas muito limitado com relação à qualidade, terminações e sobretudo tempo e custos de produção. E nem precisamos falar do custo elevado dos equipamentos...
Com o passar dos anos, novas tecnologias foram experimentadas e evoluindo, principalmente no campo de aplicação relacionado com a produção de
protótipos. Alcançando cada vez uma maior precisão no produto resultante e baixando consideravelmente os tempos e custos de produção das peças. Assim foi cunhando o termo “Protótipo Rápido” (ou em inglês Rapid Prototyping). Outro aspecto que foi se desenvolvendo com a evolução da tecnologia foi a incorporação de novos materiais e combinações destes materiais. Mas definitivamente o salto qualitativo foi o fato de que os produtos resultantes pudessem ser utilizados como funcionais, ou seja, uma inversão a partir do protótipo para a produção de produtos e/ou peças propriamente ditas.
Este foi o fato divisor de águas em dois caminhos para serem percorridos, e ambos se desenvolveram rápida e eficientemente. Por um lado, as impressoras 3D se converteram em um fenômeno que vai além das empresas ou do setor da fabricação de componentes, já que é utilizado na atualidade por diferentes usuários para gerar protótipos de urbanizações, material esportivo, vestidos ou sapatos de moda. É comum observar uma impressora 3D em escolas, universidades, centros de design e se está começando a pensar o seu potencial uso doméstico.
Por outro lado, os grandes jogadores do setor manufatureiro colocaram a lupa nesta tecnologia como ferramenta de produção. Desta forma, na atualidade, evoluiu para a incorporação de novos processos e métodos de fabricação aditiva incluindo um amplo espectro de materiais, qualidade de peça e aplicações. Poderíamos fazer então, uma primeira classificação em dois grandes grupos: fabricação aditiva para peças de plástico e para peças metálicas.
Não vamos nos aprofundar muito no primeiro, já que este não é o foco desta nota. Somente mencionaremos que hoje já estão disponíveis equipamentos industriais muito acessíveis (- de U$S10.000) que permitem produzir uma interessante gama de produtos de qualidade em diferentes materiais plásticos e poliméricos.
Fabricação de peças metálicas por aditivado
Devido à etapa “experimental” destas tecnologias se desenvolveram muitas técnicas de aditivado para a produção de peças metálicas. A seguir apresentaremos as 2 tendências que mais se desenvolveram a nível industrial.
- Fusão seletiva de leito de pó (SLM, SLS): se baseiam na fusão seletiva de uma camada de pó que foi depositado previamente. O processo é realizado dentro de uma câmera pré-aquecida e que pode ter uma atmosfera controlada para evitar a oxidação. A peça resultante é obtida a partir da fusão e posterior re-solidificação camada por camada, podendo obter peças em diferentes materiais, incluindo materiais metálicos, polímeros industriais, etc.
- Injeção direta de material (DLMD Laser Cladding): o processo consiste na fusão de um material base e na injeção de um material (tanto na forma de pó como de fio) em banho fundido. O resultado é o aporte de um material sobre um material base. Este processo é empregado tanto para a fabricação aditiva de detalhes ou estruturas sobre uma peça previamente fabricada, como para reparar zonas danificadas. A principal vantagem é o que se pode aplicar sobre peças que se fabricaram por forja, fundição, mecanização, etc. e pode aportar uma grande quantidade de materiais incluindo diferentes ligas metálicas, materiais cerâmicos e misturas de componentes.
O banho fundido é gerado pela ação localizada de um laser, o qual, além do material base funde também o material aportado. O movimento relativo entre a fonte laser e o material base dá lugar à criação de um cordão de material acrescentado e solapando destes cordões, à obtenção de uma camada de material aportado. Este processo de aporte de material pode ser empregado para a reparação de uma zona.
Exemplos das diferentes etapas de uma peça produzida em um equipamento híbrido com trabalhos de aditivado e subtrativo (mecanizado)
danificada ou gasta, para a geração de recobrimento com diferentes propriedades que o material base, ou inclusive, para a fabricação direta de peças de geometria complexa. O laser cladding combina uma grande versatilidade de formas com uma excelente integridade estrutural. Além disso, é possível empregar uma grande variedade de materiais de aportes como aço, ligas com base níquel, ligas de titânio e inclusive materiais cerâmicos. Assim, é possível combinar diferentes materiais para obter uma camada de aporte com propriedades personalizadas e especificamente adaptadas a uma aplicação concreta. Por último, cabe destacar que tanto o cabeçal óptico como o sistema de injeção de material podem ser integrados em uma máquina ferramenta convencional ou um robô.
Este é o ponto onde queríamos chegar. Mas antes de nos centrarmos nas soluções híbridas, descreveremos as vantagens e desafios para solucionar os equipamentos aditivados, para se chegar à conclusão que explica a combinação de tecnologia convencionais com as novas de aporte de material.
Vantagem e desafios para superar do “Additive Manufacturing”
Começamos pelas vantagens que aporta o aditivado, para logo ver na descrição das limitações como a combinação com sistemas tradicionais em configurações híbridas se obtém as vantagens de ambos os mundos, criando ferramentas realmente potentes.
-“Personalização em massa”: a capacidade de combinar as bondades do trabalho artesão com o volume de demanda de um grande mercado. Agora o designer é o artesão na era digital.
-Desaparecem muitas limitações geométricas, o que os designers deviam adaptar suas criações para que fossem fabricáveis, e isso permite soltar a imaginação, resolvendo problemas até agora inabordáveis;
- A fábrica digital: muito mais baseada em ativos lógicos (software) que físicos (utilidades, moldes, ferramentas), e por tanto muito mais configurável, adaptável, flexível. No entorno fabril 2.0 que permitirá que qualquer possa ser dono de uma empresa fabricante de seus próprios produtos, ou envolver-se no desenho de produtos em rede com entornos de fabricação distribuídos geograficamente.
-Processos com desperdício nulo: já que se consumirá somente o material estritamente necessários, a energia imprescindível e reduzindo drasticamente o impacto no meio-ambiente. Desafios para superar para a sua instalação definitiva:
- Baixos volumes de consumo atuais: esta situação faz que a disponibilidade de insumos, materiais, etc., é limitada e de alto custo.
- Acabamento superficial das peças e velocidade de fabricação: estes aspectos devem ser melhorados consideravelmente para alcançar níveis de produção standard.
- Qualidade de produto e repetição do processo: muitas soluções apresentam problemas de repetição, ou seja, não se pode assegurar a precisão dimensional com a que vai realizar uma peça e a seguinte. Assim, a estabilidade nas propriedades físicas do produto
Exemplos das diferentes etapas de uma peça produzida em um equipamento híbrido com trabalhos de aditivado e subtrativo (mecanizado)
(dureza, carga de rotura, metalurgia, etc.), aspecto crítico para sua homologação em determinados setores (automóvel em determinados setores (automóvel, aeronáutico, médico, etc.).
-Tamanho limitado de peças: o volume de peça máximo que se pode construir hoje em dia é bastante limitado.
-Desconhecimento por parte dos designers industriais: os designs atuais foram instruídos para conceber peças que podem ser fabricadas por métodos subtrativos ou conformativos, e isso se converte em uma limitação muito considerável para tirar todo o possível das tecnologias AM.
Soluções Híbridas: a transição que soma o melhor dos dois mundos
A partir das situações mencionadas, os principais fabricantes de equipamentos de mecanização convencional começaram a aprofundar soluções que combinassem as melhores características de ambas as tecnologias. Ou seja, lançaram centros de mecanização os quais se anexam a um cabeçal aditivado com tecnologia laser que permite várias opções adicionais ao trabalho subtrativo: desde acrescentar material para reparar imperfeições na fabricação ou reparação de peças já mecanizadas que seriam quase impossíveis (ou muito custosas) com métodos tradicionais; até a produção de peças diretas com ligas especiais e características geométricas muito complexas, que podem ser terminadas e aperfeiçoadas por um método mecanizado tradicional para alcançar as qualidades desejadas.
Existem hoje equipamentos que somam o melhor das tecnologias subtrativas (arranque de lascas) e aditivas (aporte de materiais), alcançando soluções ótimas de frente com um mundo que exige cada vez mais precisão, eficiência e por sua vez flexibilidade e customização
Referências
- “La fabricación aditiva, tecnología avanzada para el diseño y desarrollo de productos” – Manuel Zahera / Fundación COTEC – XVI Congreso Internacional de Ingeniería de Proyectos- Valencia, julho de 2014.
-“Fabricación aditiva: ¿Qué es cada tecnología?’ Eneko Ukar, Aitzol Lamikiz, Depto. De Ingeniería Mecánica de la Universidad del País Vasco – junho de 2015.
-INTERNATIONAL CONFERENCE ON ADDITIVE MANUFACTURING – 6 de outubro de 2015/ EMO Milão 2015 Fiera Milano Rho.